Why the right prefab system can speed up toilet block installation by 30%
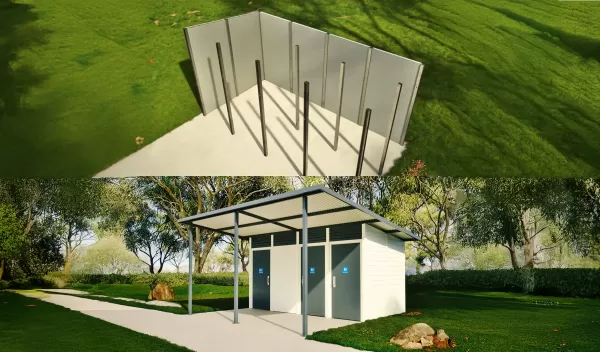
Not all prefabricated modular toilet block systems are the same.
Understanding this, and then choosing appropriately, can save councils, installers and contractors weeks of construction time.
Instead of building everything on-site from small components, prefab systems bring advantages of modern mass-manufacturing and economies of scale.
All prefab systems — even flatpack ones — offer distinct advantages over traditional construction methods, particularly in terms of speed of construction, labour requirements, staging, and site cleanliness.
This shift from traditional building methods offers numerous cost-efficiency benefits that are transforming the construction landscape.
Not all 'prefab' systems are equal
Many suppliers will sell their installation methods as ‘pre-fabricated' or 'modular’ however in reality they lack true modularity.
Components arrive as a “kit” that are bundles of separate building materials that require substantial assembly (typically they are all screwed together) before they can be mounted to the pad, or hung on the building frame.
What’s more, these prefab flatpack installations typically require at least two concreting steps — something that has substantial lengthens install time.
These modular flatpack systems typically use a lengthy 11-step process:
1. Services pre-lay: workers pre-lay all the plumbing and electrical services.
2. Earthworks and sand pad: the building pad area is excavated and sand fill formed and compacted.
3. Footing excavation: individual footings for each column are excavated.
4. Footing pour and cure: concrete is poured into the footings and then allowed to cure.
5. Column and structure installation: columns are installed onto the cured footings, and the structure is fitted to columns to ensure squareness of the entire structure.
6. Concrete pad pour and cure: The concrete pad is poured. Trowelling and levelling concrete around multiple columns is a challenging, time-consuming task. The newly laid concrete must also cure.
7. Building framing: framing sections of the toilet facility are installed: screwed together and into the columns.
8. Internal and external sheeting: Internal and external cladding is screwed onto the frames and columns.
9. Roofing: installation of roof framing, sheeting and trims.
10. Internal fit-out: installation of internal fixtures and fittings.
11. Commissioning and handover: Testing of all functions, complete building audit, and handover to client.
What ought true modular prefab look like?
True modular pre-fab does as much as possible can offsite in order to leverage the efficiency and accuracy of industrial processes.
This compresses construction into a highly efficient seven-step process:
1. Services pre-lay: workers pre-lay all the plumbing and electrical services.
2. Earthworks and sand pad: the building pad area is excavated and sand fill formed and compacted.
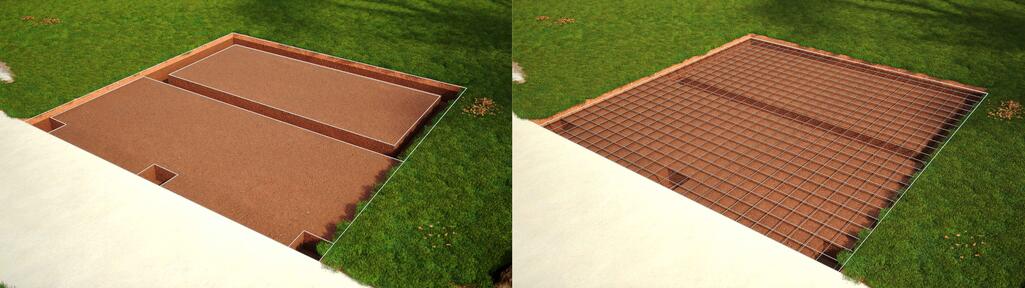
3. Concrete pad pour and cure: the concrete pad is poured, including thickening areas for column locations. Without columns to interfere trowelling and levelling is fast and easy. There is only one curing period.
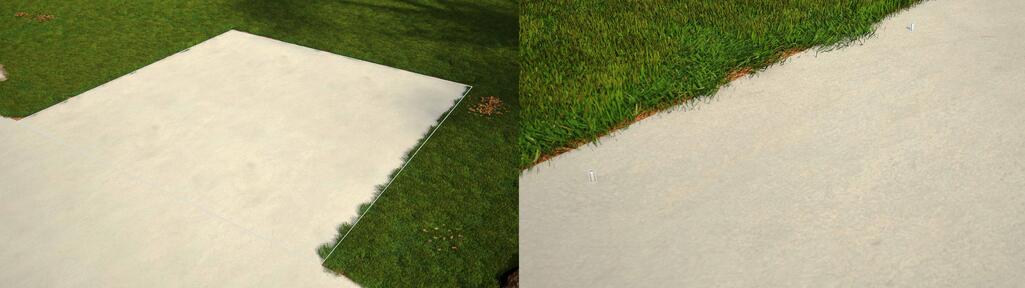
4. Prefab wall panel and column installation: workers install prefabricated modular panels that are internally and externally pre-clad and require no additional assembly; doors are pre-hung in frames. Installation is a simple bolt-together process.
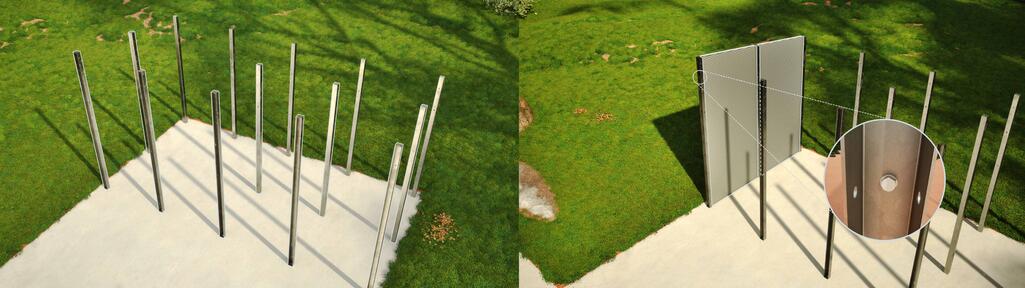
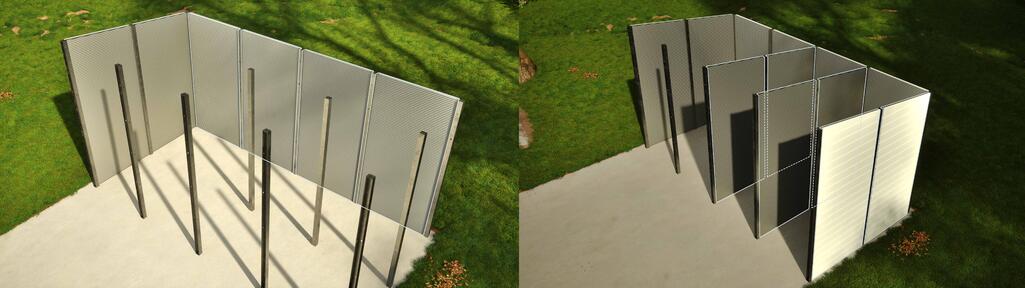
5. Roofing: installation of roof framing, sheeting and trims.
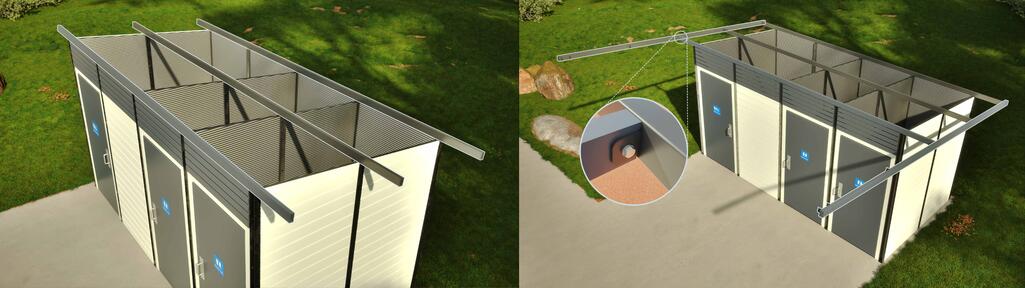
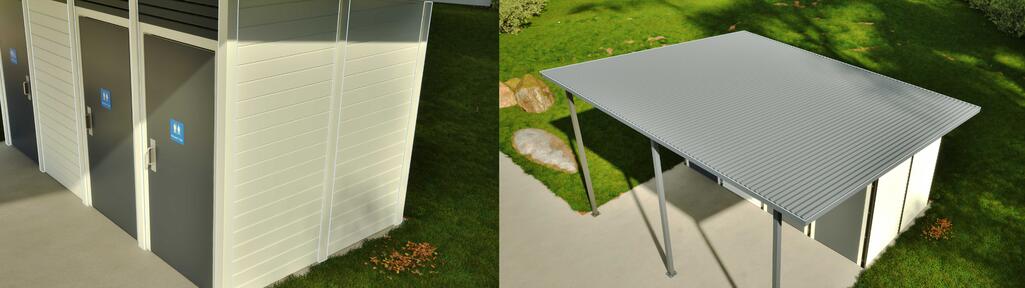
6. Internal fit-out: installation of internal fixtures and fittings.
7. Commissioning and handover: Testing of all functions, complete building audit, and handover to client.
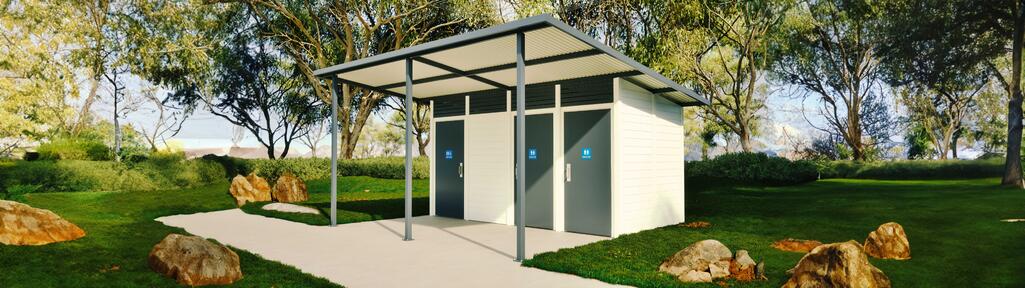
As mentioned, the problem is that juggling the creation of footings, installation of columns, concreting the pad, and bracing and laying plumbing and pipe lines remains a complicated, multi-step process that is neither simple, nor fast.
Only after this is complete can installers come back and begin to install the framework of the toilet block. And because the shelter frame has cast-in legs, squaring off all these columns can be time consuming.
Plus, as discussed earlier, there’s little that’s truly modular or pre-fabricated about the supplied frame kits: frame modules are supplied separate from their cladding and everything needs to be individually screwed together and then installed into place.
Not only is this time-consuming, it leaves a lot of room for installer error.
Let’s make your next project a success
Fill out the form below to start the conversation with our experienced team.
True modular prefab is as much as 30% faster than flatpack (and streets ahead of traditional methods)
Where this system differs is that it’s designed to require minimal connections on site.
Instead, it relies on the use of strong surface mounts to the concrete pad and simple bolt-together construction. Thus, there is no need to cast columns — or any part of the building, except services — in concrete.
Therefore, you can task your plumber with the plumbing pre-lay set, then give the concreter a single concreting set.
Once those two trades are done and the pad is cured, building erection and installation can be performed in a single site mobilisation: you have a flat pad that installers can just screw straight into to put up the building frame.
What makes this even faster is that the complex work is performed offsite: panels are pre-clad inside and out, and doors pre-hung in their frames.
It's simply a matter of bolting down your columns, standing up the pre-clad panels, completing your roofing, then putting in the internal fixtures.
Pre-fabrication improves accuracy, minimises both the volume of waste produced on-site and the amount of disruption to the community, and generally reduces the exposure to site-based project risks such as installer error, or weather.
What’s more, it doesn’t require experienced, skilled labour.
For an LGA, that means it can be performed by a local builder, keeping money within the community. And for the contractor/builder, there is typically more margin in the job.
Finally, it’s easy to individually remove and replace panels in event of major damage such as a vehicle impact, or acts of extreme vandalism.
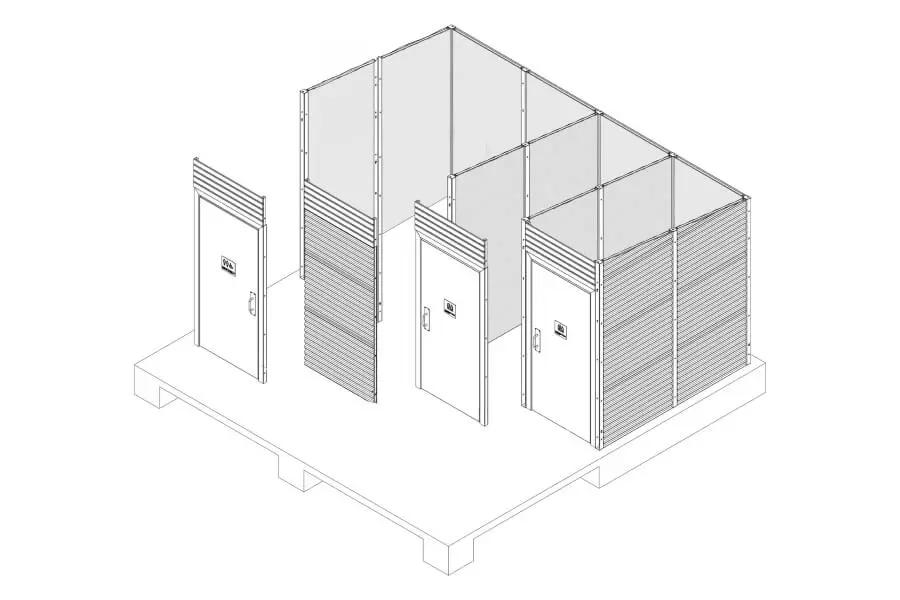
The allure of the “drop-in” solution
Given all the above, it might seem attractive to take prefabrication to its ultimate end-point: an entire facility that is prefabricated off-site, then transported in and “simply” craned into place.
Unfortunately, there’s nothing simple about shifting to this sort of scale.
Once you have something larger than the truck transporting it, you have to deal with oversized loads.
The logistics are demanding and expensive: from getting permits to shutting down roads and laneways, organising police escorts, and ensuring there’s sufficient vertical and horizontal clearance at every point of transport. Site access itself must be extremely good and you’ll require specialist expertise.
Even if you go smaller — no larger than will fit on a truck — you’re suddenly limited in the designs you can implement. Drop-in buildings must be designed around crane-able module sizes.
Your solution might no longer be optimal for the site, or for community needs.
You give up a great deal of flexibility for not a lot of gain.
Exploring your options with Modus
Prefabricated modular toilet block construction has greatly gained popularity in recent years due to its numerous benefits, including cost-efficiency, faster construction time, and reduced waste.
But to maximise its primary advantage — reduced construction time — you need to ensure you’re working with a supplier who is fully committed to the pre-fabricated methodology.
Only then can you reap the benefits: projects that are completed 30% to 50% faster with an accelerated timeline that directly translates into cost savings, smaller labour requirements and lower on-site overheads.
While these suggestions offer a foundation for action, it’s crucial to recognise that each project is distinct. We are experts in prefabricated systems and lead the way in the approach.
So if you’re unsure about the best way forward for your next project, call us on 1300 945 930 or book a project consultation below.